ERO Joint® mechanically assembled belts are used on assembly lines in the automotive industry. Where every minute of downtime counts, ERO Joint® saves hours of downtime by replacing belts quickly.
Timing belts with ERO Joint® mechanical connections are mainly found on sheet metal conveyors, before and after stamping, on roller and transfer tables, and in other locations where belt stress is high.
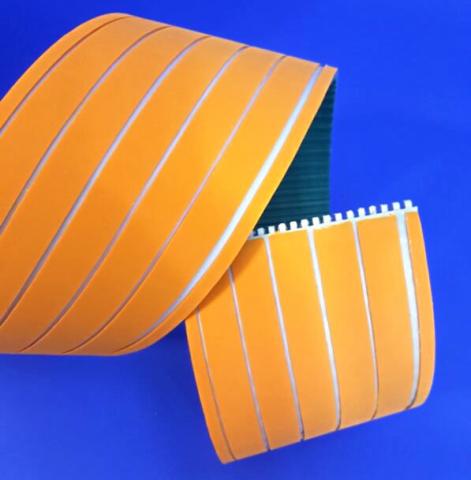
Sheet metal destacker Belt
Sheet metal destacker Belt / Linatril-coated T10 belts. Several belts are used in parallel. ERO Joint® HP allows quick replacement of one of the belts in the event of an accident on a press.
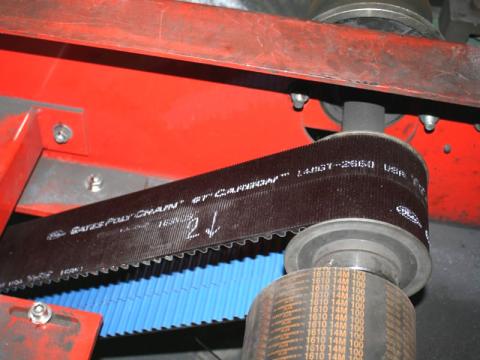
Poly Chain® GT Carbon™ ERO Joint® Ultimate
Poly Chain® GT Carbon™ ERO Joint® Ultimate 14M belts used to drive a roller table on a Renault production site. Replacing such a Belt can normally take over an hour. With ERO Joint®, replacement takes just 20 minutes.
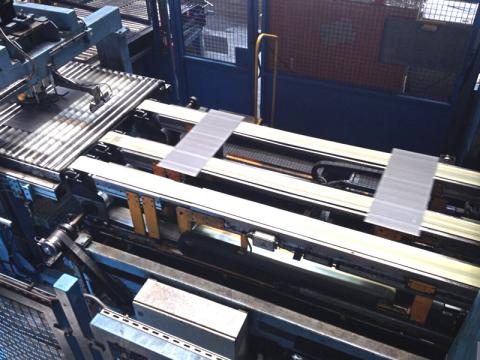
T10 ERO Joint® WT for sheet metal conveying
These 2mm-thick polyurethane-coated belts are ideal for transporting sheet metal. ERO Joint WT allows particularly rapid replacement, without dismantling the entire installation.
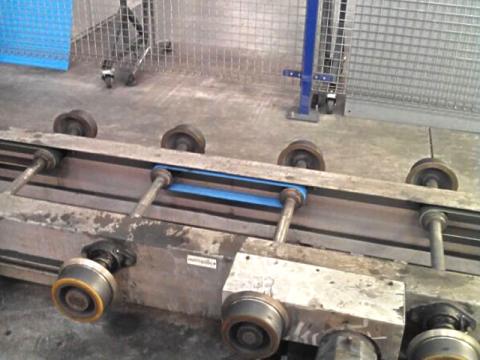
ERO Joint® Flat belt on skid conveyor
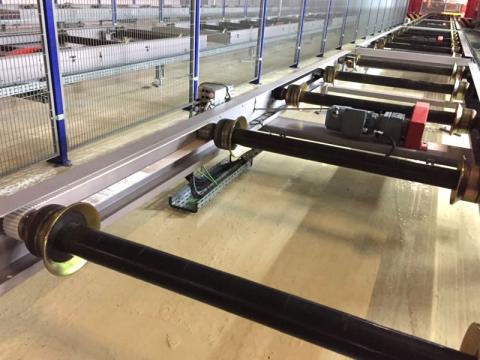
ERO Joint® HP Flat belt on skid conveyor
Some roller tables are equipped with flat belts. The use of an AT10 Timing belt with a grooved and reversed coating makes it possible to replace the worn flat belt in 10 minutes.
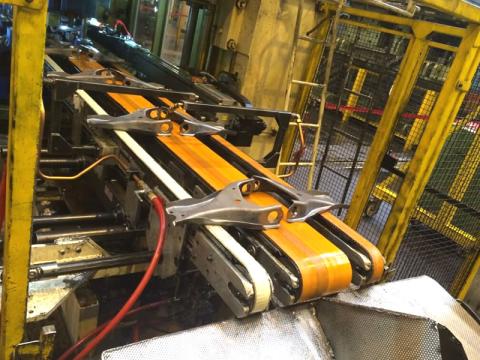
T10 ERO Joint® with PU coating
The ideal solution for transporting metal parts in a stamping shop.
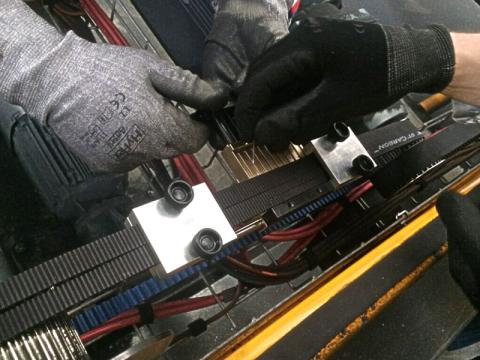
Poly Chain® GT Carbon™ ERO Joint® Ultimate mounted on a roller table
Using rod tensioning and insertion tooling, this 8M Belt mounted on a Stellantis site enables the replacement of a broken Belt in 15mn instead of an intervention of more than an hour in normal configuration.
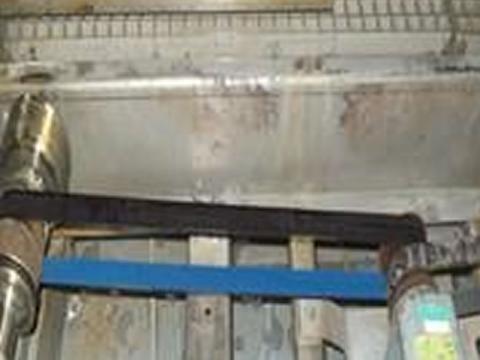
Poly Chain® GT Carbon™ ERO Joint® Ultimate (silicone-free) mounted on a roller table in the paint shop.
For paint shops in the automotive sector, belts can be made "silicon free". After production, they are thoroughly cleaned to remove all traces of silicone.
